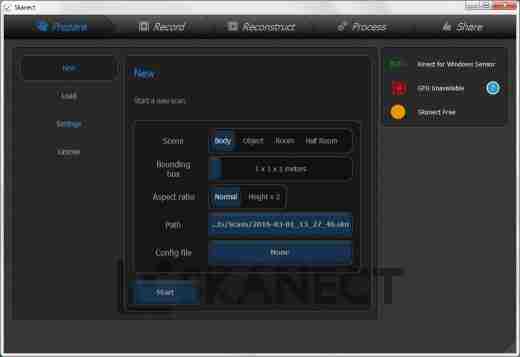 |
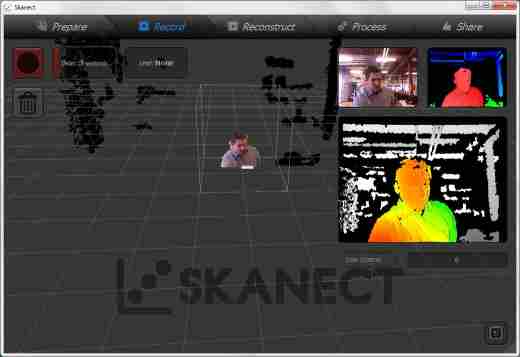 |
Figure 21: Generating a New Scan with Skanect |
Figure 22: Ready to Record Myself with Skanect |
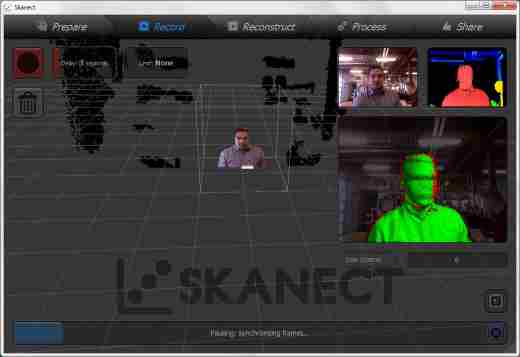 |
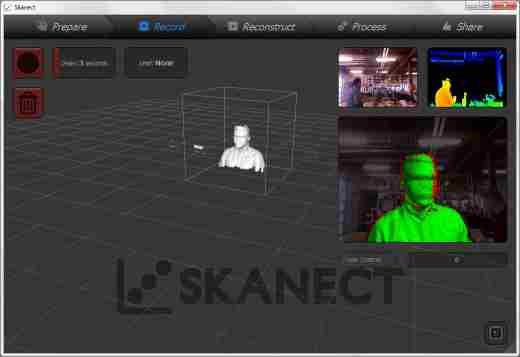 |
Figure 23: Processing Scan into 3D Model |
Figure 24: 3D Model Generated with Kinect and Skanect |
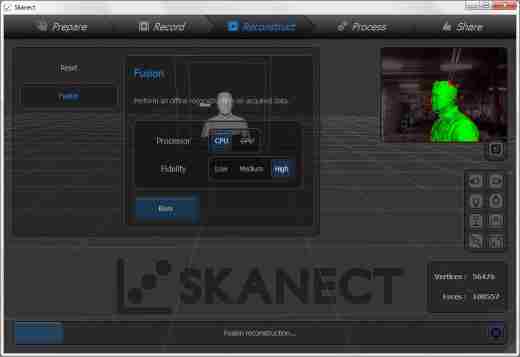 |
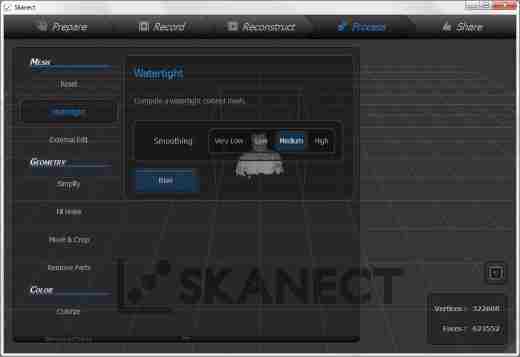 |
Figure 25: Editing Image to Generate Smoother Model |
Figure 26: Filling in Holes of Model to Generate Solid 3D Model |
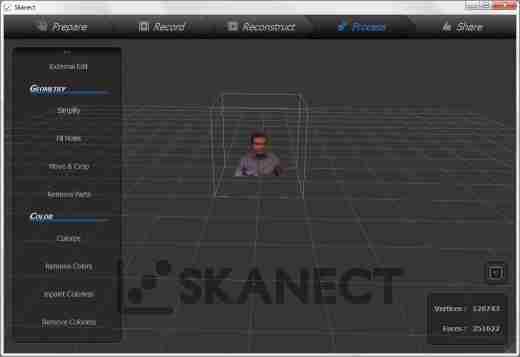 |
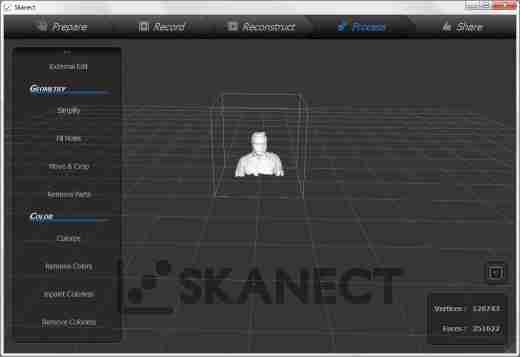 |
Figure 27: Final 3D Model Produced by Skanect in Color |
Figure 28: Final 3D Model Produced by Skanect in White |